If you aren’t employing the correct check valve for your water application industry, significant accidents may occur due to high-pressure water gushing the reverse way. Therefore, selecting the appropriate check valve for your water industry is essential.
What are the three types of check valves for water application? The top three check valves recommended for your water application system are the swing check valve, the double door check valve, and the butterfly check valve.
To differentiate between these three check valves and select one suitable for your water application needs- keep reading!
What Is a Check Valve?
A check valve is an automated device commonly known as a ‘one-way’ valve.
True to its name, this ‘one-way’ valve only allows water or liquid to flow in one direction and prevents it from washing back in the reverse direction.
The function of a check valve is essential in the long life of your water application system because preventing the reflux of water in the reverse direction prevents contamination in the case of infected water.
If a check valve did not prevent the backflow of such contaminated water, it would lead to the upstream flow also getting spoiled.
The importance of a check valve can be highlighted by considering a sewage line- a check valve would ensure that sewage would be allowed to leave the pipelines but not re-enter.
The Three Types of Check Valves for Water Application Systems
Now that you are acquainted with the workings of check valves, it’s time to introduce you to the three most popular check valves for water application systems.
Swing Check Valve
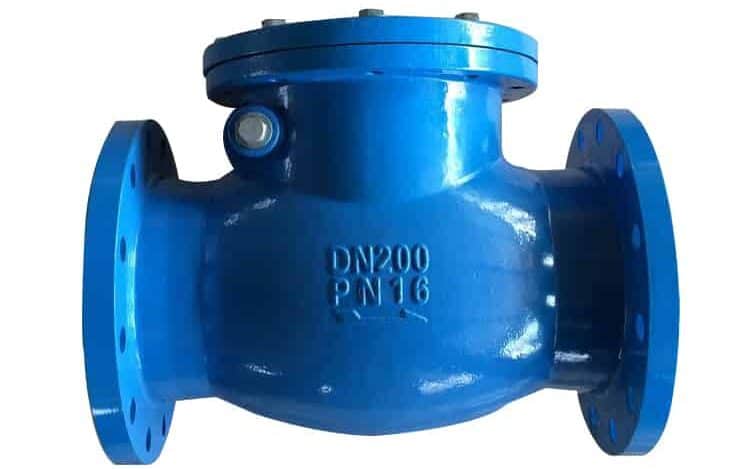
Naturally, a swing check valve is in charge of allowing a one-way flow of water or gas within a system.
A swing check valve can make this happen because it has a disc that swings on a hinge, much like a door. Therefore, when it has to allow a medium in, it revolves open and shuts closed afterward to prevent backflow.
Because swing check valves depend on the swinging of their discs or flappers to function, they can only be used in horizontal or vertically upward pressure pipelines.
Therefore, the specialty of a swing check valve is managing the high horizontal flow and pressure within a system and catering to significant flow capacities. This is why they are most commonly used in wastewater treatment and water pumping.
However, swing check valves are generally made of polyvinyl chloride (PVC) or metal and are most suitable for systems that receive a constant flow of fluid- much like toilet drainage.
If you are looking for an inexpensive and easy-to-maintain check valve for your horizontal lines that does not require external power- this is the perfect option for your system!
Double Door Check Valves
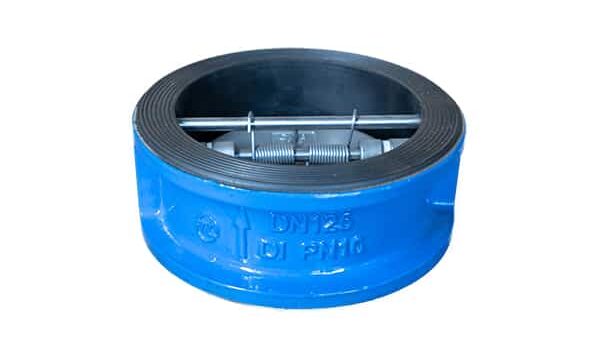
Double door check valves carry out the same vital functions as other check valve variations- to prevent backflow of water.
The double door check valve consists of shutoff valves and minuscule ball valves at each end of the check valve. Furthermore, it contains two independently operating spring check valves.
A double door check valve can be more beneficial than a single door check valve because one of the check valves will still work and provide a seal even if the other is jammed or damaged.
Moreover, when one of the check valves shuts, it reduces the pressure differential of the other check valve, improving the quality of sealing and preventing leakage.
A double-door check valve is suitable for industries that deal with pristine water and gas in their systems. Such industries include HVAC systems, refineries, petrochemical, and gas liquefaction.
Double Door Check Valves vs. Swing Check Valves
A double door check valve has various advantages over a swing check valve.
A double door check valve is more cost-efficient and is equipped with non-slam properties which are not present in a full body swing check valve.
Furthermore, it has a low-weight body and small laying length, which initially makes it more affordable and accessible to install than a full-body swing check valve.
These features also mean that the double door check valve requires less space than full body swing check valves and hence is more appropriate for your system if your system has a space constraint.
Moreover, the construction of a double door check valve allows it to be better and quicker at closing than a swing check valve because it is equipped with coiled springs, which assist in shutting its bracketed doors.
However, like the swing check valves, double door check valves are not ideal for water hammering but will perform a better job.
Butterfly Check Valves
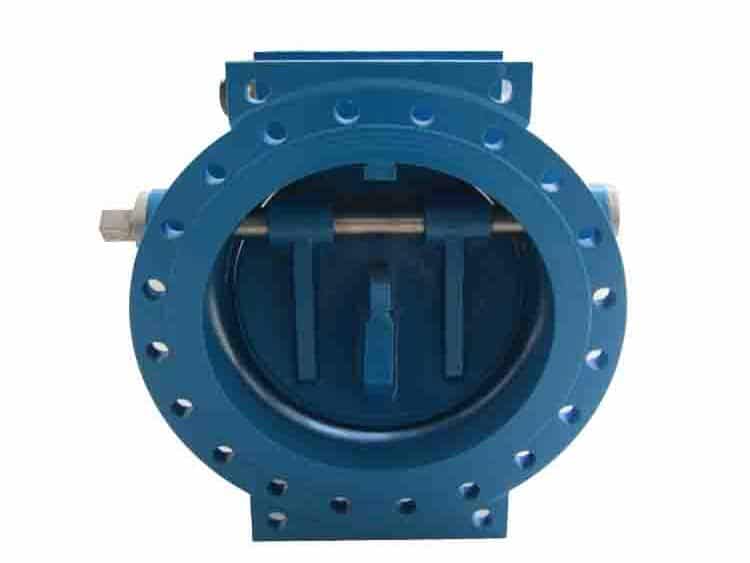
Butterfly check valves are often thought to be the same as standard butterfly valves- however, it is essential to note that they differ from one another!
Butterfly check valves have similar seating positions and flow characteristics to general butterfly valves and are, therefore, most suitable for systems employing butterfly valves.
Furthermore, the build of a butterfly valve is such that it accommodates adequate space for the butterfly valve disc within the check valve and therefore eliminates the need to install spacers within the system.
Butterfly check valves are reliant on pressure differentials to operate automatically.
Consequently, these butterfly check valves open when the suction pressure outweighs the outlet pressure. On the other hand, the butterfly check valves shut when the outlet pressure outweighs the suction pressure, when there is a reverse flow of fluid or when the pump halts.
Naturally, when the check valve shuts, it prevents backflows and fulfills its primary function as a ‘check valve.’
Advantages of Using Butterfly Check Valves
There are numerous other advantages that butterfly check valves provide:
- Their relatively quiet application makes them a viable check valve to use in systems where a high noise level is avoided.
- Their coherent design and build make them easy to install in larger diameters- up to 72 inches.
- The butterfly check valves have a layout that allows for the installation of seat liners of various materials- this makes it possible to build an inexpensive corrosive-free butterfly check valve that does not require high-quality metal or alloy seat fittings.
- Unlike other check valves, butterfly check valves can be installed in horizontal and vertical pipeline systems, with both an upward and downward vertical pressure flow.
How Does a Check Valve Perform Its Function?
To understand how a check valve fulfills its function, you will need to understand the concept of an ‘upstream pressure,’ also commonly known as a valve’s ‘cracking pressure.’
The pressure differential between the system’s inlet and outlet creates ‘Upstream pressure.’
A check valve requires a minimum upstream pressure or cracking pressure to unlatch the valve and let the median pass before shutting again to prevent backflow.
The water application system produces this minimum upstream pressure. Therefore, you must ensure that your water application system can make the cracking pressure required by your chosen check valve- as different types and variations of check valves need different levels of cracking pressure.
What Happens if Your Water Application System Cannot Produce the Required Cracking Pressure?
If your water application system cannot produce the required minimum upstream pressure, or if there is backward pressure, the check valve will automatically shut.
Check valves usually come equipped with a diaphragm, ball, disc, or gate, which are compressed against the seal to aid in closing the valve.
Moreover, the check valve can use a spring or gravity to aid in closing the valve, especially when the cracking pressure is not up to par.
Conclusion
By now, we’re sure you have garnered all the ins and outs of these three check valves and are confident of which one is the perfect match for your water application system.
To clear up any queries, contact us or do a more in-depth deep dive into the valve world through our blog.